Piston Filling Machine
Home » Liquid Filling Machines » Piston Filling Machine
Piston Filling Machine: the latest technology
Depending on the application sometimes Flowmeters is not the best technology to guarantee an accurate dose or to keep the nature of the product without changes that might impact on the quality of the final product. There are some special applications where Piston Filling Machinery (either with piston pumps built in Ceramic or in Stainless Steel) are the most recommended solution: when an accurated control of the product flow is required, swirl and multistream products, hot filling applications, microdosing high accuracy and stability.
Main Benefits
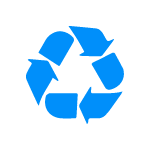
Continous product recirculation
The Filler’s product path is a closed loop that enables to keep the product in continuous recirculation to avoid sedimentation of solid particles in the solution. Total absence of dead end zones. After a prolonged stop pistons return the product back to the loop.
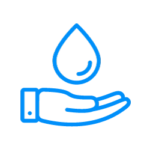
Excellent Accuracy
Piston Pumps are designed according to the max bottle size to be filled. Ceramic Piston Technology allows to manufacture small sleeves and pistons without gaskets and seals to deliver Micro dosis with an excellent accuracy.
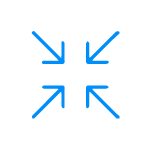
Reduced footprint
Filler diameter is smaller compared with the traditional Flowmeter Fillers. Standard pitch is 110 mm, a Rotary Filler for 200 upm is a primitive diameter of 420 upm. Compact Design and reduced footprint.
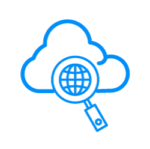
Real Time Production Management
With Mengibar Downtime Tracking and Real-Time Production Management the line operator has control over the whole packaging process. Features include machine status, downtime tracking with root cause identification, quality monitoring, automated alerts and notifications, OEE performance, meaningful trend analysis, individual energy consumption, safety management, etc. An Ethernet connection links to the SCADA system’s database and software programs providing trending, diagnostic data and management information. Micro dosis with an excellent accuracy.
Markets & Applications
Versatile Machinery Solutions
At Mengibar, we engineer versatile liquid filling and capping machinery. Our solutions encompass hot liquid filling for embedding solids within containers, and even multistream filling for creating artistic patterns on product surfaces.
Jacketed Product Path
HOT LIQUID FILLING FOR SOLID PRODUCTS
When engineering becomes art