Filling & Capping Monoblock for Hair Care and Body Care
Home » Case studies » Applications » Hair & Body Care » Filling & Capping Monoblock for Hair Care and Body Care
Project Description
Filling and Capping Monoblock for different formats of Hair Care and Body Care at 220 units per minute.
The project has been commissioned by an innovative and globally well-known manufacturer of Cosmetics and Home Care products in North America.
The project faced significant challenges that needed to be overcome.
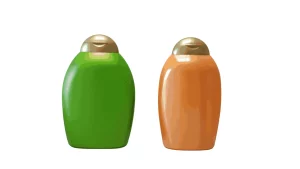
The Challenge
The challenges include achieving an accurate and consistent filling of highly viscous products, implementing a rapid and efficient cleaning system post-product changeovers or at the end of a production shifts, quick changes between bottle and cap formats, and an accurate capping of snap-on oriented oval-shaped caps with minimal errors.
The customer emphasized the need for a compact solution with a minimal factory footprint.
How did Mengibar solve it?
To ensure a consistent filling, Mengibar has developed a technology that ensures accurate filling through specially designed nozzles, preventing dripping. Mengibar Filling technology focuses on achieving the highest accuracy never-before-seen by closely monitoring both internal and external dynamics with rapid readings at each filling station in real time. The technology, named Smartflow, detects flow variations, maintains unchanging pressure and flow conditions, and regulates the optimal flow rate at every filling station.
For a quick and easy cleaning system, Mengibar has introduced several solutions. The Monoblock‘s design incorporates easily accessible and removable components for efficient cleaning. Additionally, a fully integrated stationary 360º collecting tray CIP (Cleaning-In-Place) system automates the cleaning process, reducing downtime between product changeovers or at the end of a production shift. The material of the collecting tray is designed to resist product adhesion, facilitating easier cleaning.
Regarding the rapid changeover of bottle and cap formats, the machine features a quick and tool-free changeovers. The entire process is operated through a user-friendly interactive H.M.I. touch panel, supported by documentation to guide operators through the changeover process.
By overcoming these challenges, Mengibar enhances the efficiency, reliability, and flexibility of the Filling and Capping line provided to this customer, meeting their specific outlined needs.
Regular collaboration with customers and ongoing innovation remains key for Mengibar to stay ahead in the competitive manufacturing environment.
We invite you to watch the following video where we explain in more detail how we solved the case study.