Monoblock Filling & Capping for Tire Sealant
Home » Case studies » Applications » Car Care » Monoblock Filling & Capping for Tire Sealant
Project Description
This project involves the implementation of a new Filling and Capping Monoblock for a leading US Chemical company operating in the Automotive sector, well-known for its Tire Sealant solutions.
The customer’s goal is to increase their intermediate linear line by implementing a continuous motion rotary system, enabling a production rate of 75 units per minute. This improvement must prioritize maximum accuracy, efficiency and reduce the cleaning time required for the current line.
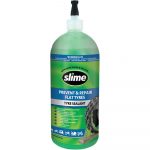
The Challenge
The challenge began with the product to be filled, which presented significant obstacles in terms of filling and cleaning due to the high viscosity caused by the presence of bits and fibers. Maintaining consistent filling while minimizing the risk of contamination was also a major difficulty in this project.
To overcome these challenges, Mengibar has developed a solution that addresses key issues in the filling process for this type of product. Furthermore, the customer emphasized the importance of reducing the cleaning time of their current filling line, and Mengibar successfully addressed this as well.
How did Mengibar solve it?
Mengibar’s solution incorporates specially designed viscous filling heads that enable a consistent and uniform flow of the product. This not only reduces filling time but also prevents potential splashing, ensuring precision and minimizing waste.
The machine features a sanitary design with non-contact nozzles, eliminating the risk of cross-contamination. By removing the presence of mesh or flow restrictors in the nozzles, maintenance efforts are significantly reduced, contributing to improved productivity.
Furthermore, Mengibar offered a state-of-the-art Cleaning in Place (CIP) System that includes a 360º collecting tray. This innovative design eliminates the need for manual intervention before and after the cleaning cycle. As a result, product changeovers are faster, the duration of the CIP cycle is reduced, and overall machine efficiency is enhanced.
We invite you to watch the following video where we explain in more detail how we solved the case study.