Llenado y Tapado Monoblock para sellador de neumáticos
Home » Case studies » Aplicaciones » Cuidado del Automóvil » Llenado y Tapado Monoblock para sellador de neumáticos
Descripción del Proyecto
Este proyecto consiste en la implantación de un nuevo monoblock de llenado y tapado para una empresa química estadounidense líder en el sector de la automoción, conocida por sus soluciones de sellado de neumáticos.
El objetivo del cliente es aumentar su línea lineal intermedia mediante la implantación de un sistema rotativo de movimiento continuo, que permita alcanzar un ritmo de producción de 75 unidades por minuto. Esta mejora debe priorizar la máxima precisión y eficacia y reducir el tiempo de limpieza necesario para la línea actual.
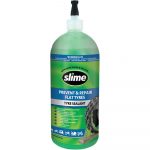
El desafío
El reto comenzó con el producto a envasar, que presentaba importantes obstáculos en términos de llenado y limpieza debido a la alta viscosidad causada por la presencia de trozos y fibras. Mantener un relleno homogéneo minimizando al mismo tiempo el riesgo de contaminación fue también una de las principales dificultades de este proyecto.
Para superar estos retos, Mengibar ha desarrollado una solución que aborda cuestiones clave en el proceso de llenado de este tipo de productos. Además, el cliente hizo hincapié en la importancia de reducir el tiempo de limpieza de su línea de llenado actual, y Mengibar también lo abordó con éxito.
¿Cómo lo resolvió Mengibar?
La solución de Mengibar incorpora cabezales de llenado viscosos especialmente diseñados que permiten un flujo constante y uniforme del producto. Esto no sólo reduce el tiempo de llenado, sino que también evita posibles salpicaduras, garantizando la precisión y minimizando los residuos.
La máquina presenta un diseño sanitario con boquillas sin contacto, lo que elimina el riesgo de contaminación cruzada. Al eliminar la presencia de mallas o limitadores de caudal en las boquillas, los esfuerzos de mantenimiento se reducen significativamente, lo que contribuye a mejorar la productividad.
Además, Mengibar ofreció un sistema de limpieza in situ (CIP) de última generación que incluye una bandeja colectora de 360º. Este innovador diseño elimina la necesidad de intervención manual antes y después del ciclo de limpieza. Como resultado, los cambios de producto son más rápidos, se reduce la duración del ciclo CIP y se mejora la eficiencia general de la máquina.
Le invitamos a ver el siguiente vídeo en el que explicamos con más detalle cómo resolvimos el caso de éxito.