Multifunctional Indexing Monoblock for Airfresheners and Insect Control
Home » Case studies » Applications » Air Freshener » Multifunctional Indexing Monoblock for Airfresheners and Insect Control
Project Description
The project focused on finding a tailor-made solution for Filling, and Capping, offering a new alternative to high-speed packaging lines for Personal Care and Home Care products targeted at markets and customers seeking lower-speed lines.
This innovative equipment enables various consecutive operations through intermittent movement facilitated by a central starwheel, allowing containers to pass through all stations until the packaging process is complete.
In this specific case, the configured Indexing Monoblock is designed for packaging home air fresheners at 50 units per minute (upm). These products are known for being aggressive towards elastomers and involve a complex packaging process that hinders efficient manual operations. Hence, even at lower speeds, an automatic machine is justified.
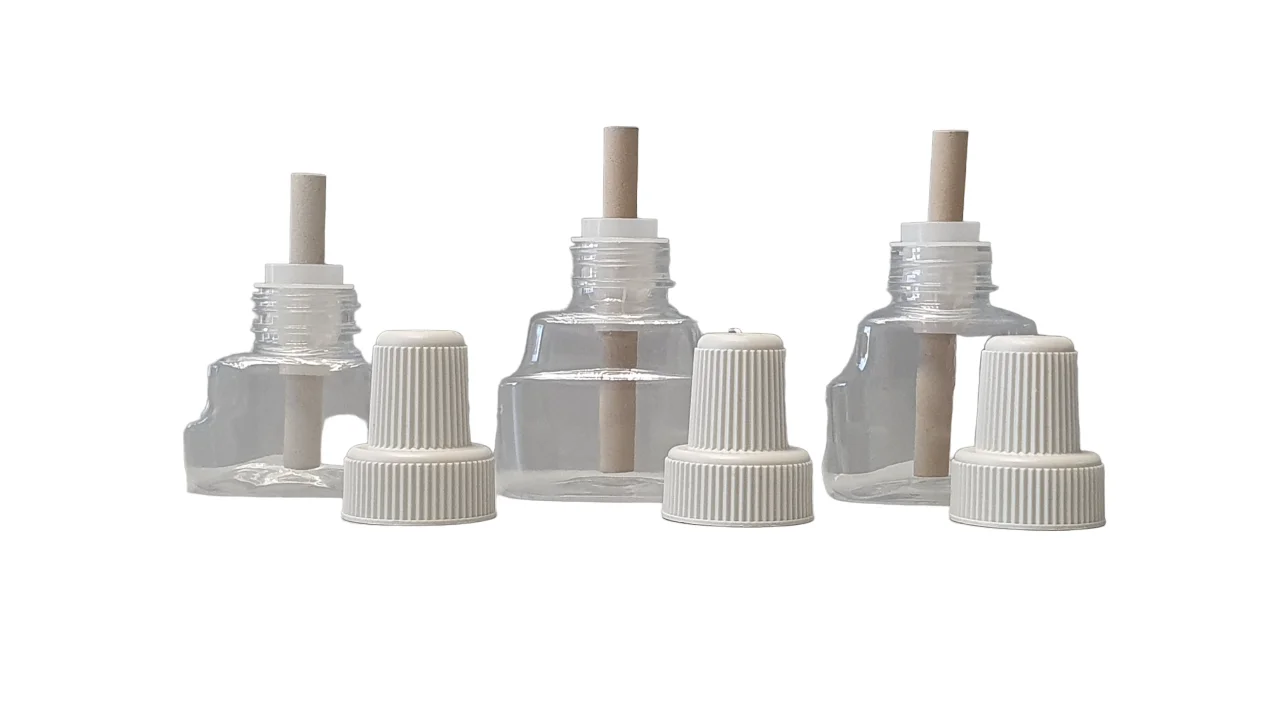
The Challenge
Our challenge was not only to design a new fully automated line for speeds of up to 50 upm but also to make it modular. The goal was to create a system adaptable to any other application, more or less complex, without the need to redesign a significant portion of the project’s engineering.
The final customer had no prior Mengibar equipment but was familiar with our reputation from other plants within the company in different countries. Although this machinery segment was not Mengibar’s typical domain, we had to compete at a different level than usual, where, due to lower speeds, efficiency and productivity do not usually represent a competitive advantage.
Mengibar successfully secured the order by presenting a machine that met the customer’s expectations with a significantly higher quality level than the competition, incorporating our experience in projects for similar applications at 200 and 300 upm.
How did Mengibar solve it?
Modular Monoblock: Mengibar developed a modular system capable of performing the simplest (filling and capping) to the most complex operations (filling, sealing, capping, pre-assembly of components, quality control, and rejection of non-conforming products) in a single machine, utilizing a single intermittent star with the capacity to adapt to any present or future operation.
Flexibility: Mengibar designs and manufactures its own automatic feeding systems for caps, seals, and any other bulk-fed components. This enables easy integration of all line components and peripherals. One supplier for all operations:
- Filling.
- Pre-assembly (Wick + Seal).
- Screw capping.
- Automatic feeding of containers, wicks, seals, and caps.
- Quality control and rejection of non-conforming containers.
Strategic Materials: Electric air fresheners and insecticides contain solvents and essential oils that can damage seals and other elastomers. Leveraging our experience and developments for similar products in filling and capping Monoblocks, Mengibar designed an efficient volumetric filling system more precise than any other in the market (flow meters, net weight, or level) with ceramic contact parts and a complete absence of elastomers.
We invite you to watch the following video where we explain in more detail how we solved the case study.