Filling and Capping Machine for Corrosive WC Cleaner
Home » Case studies » Applications » Household » Filling and Capping Machine for Corrosive WC Cleaner
Project Description
Filling, plug inserting and screw Capping Monoblock for highly corrosive bleach based WC cleaner at 150 upm. The Monoblock had to work in the same machine with both thin and viscous WC gels (all of them with high pH levels).
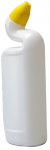
What was Client's need?
This type of filling machine for corrosive WC cleaner is typically a ‘low cost’ machine built in Plastic with absolutely no durability nor accuracy compared with a Filling Machine using superior resistance materials. We were required to build a robust machine using materials with superior corrosion resistance (not in plastic) at a very competitive price due that our competitor was proposing a plastic machine.
Besides this, during the design of the filling machine we discovered that the angle-neck bottle had different angles depending on the mould. So, an accurate and flexible way to incline the bottle was required.
How did Mengibar solve it?
Materials with superior corrosion resistance and polyamide coatings are used to ensure the durability and strength of all materials and components.
- Filling machine base frame is built in AISI-316L stainless ateel with a top cover protection in polypropylene and clear guardings in transparent Makrolon AR.
- On top of the frame, base supports and bottle sliding guide are built in AISI-316L stainless steel + PA11 coated.
- AISI-316L stainless steel + PA11 conveyor with polypropylene chain.
- AISI-316L stainless steel + PA11 filling carousel, positive pressure in product tank, manifold, circuit and nozzles in Hastelloy.
- 360º product collection tray in Stainless Steel AISI-316L stainless steel + PA11 coated.
- Capping carousel with AISI-316L stainless steel column, bottom section covered in PVC, and AISI-316L stainless steel + PA11 protections.
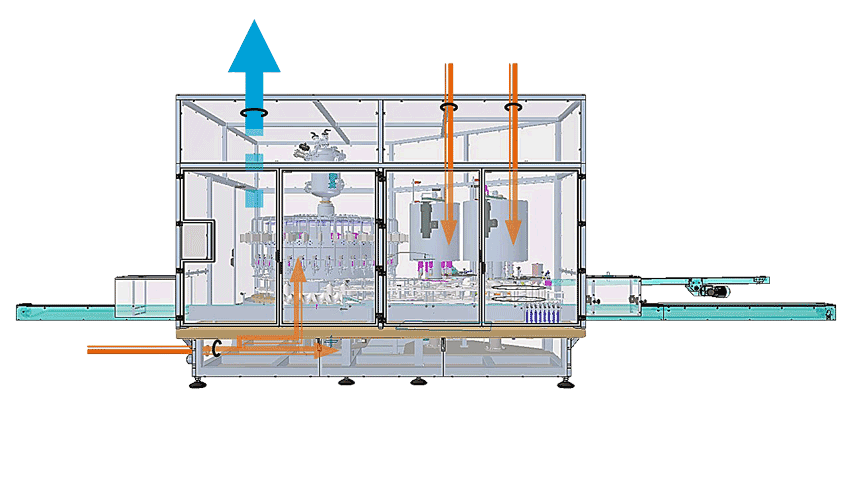
In addition, the Monoblock was equipped with a continuous ventilation system which involves the machine base frame, filling carousel and capping carousels. All these elements are isolated from the corrosive atmosphere and over pressurized to prevent from corrosion all the elements inside: drives, gears, electricals, bushings, electronics, etc.
Machine base and carrusel presurization provides 100 renewals per hour at at minimum flow of 600 cubic meters per hour. The air extraction system located on top of the safety guarding guarantees 82 to 120 renewals per hour and a continuous flow of 2.400 cubic meters per hour.
Gas detectors are installed to stop the production of the filling machine in case that any of these ventilating systems fails.
We invite you to watch the following video where we explain in more detail how we solved the case study.