Máquinas de llenado de líquidos
Home » Máquinas de llenado de líquidos » Máquinas de llenado de líquidos
Tecnología revolucionaria de Llenado de Líquidos
Las máquinas de llenado de líquidos MagFlow y MassFlow de Mengibar representan la alternativa más innovadora para llenar una amplia gama de productos: desde líquidos finos y espumosos hasta líquidos altamente viscosos, con una precisión y eficiencia de llenado nunca antes vista.
Además permite el seguimiento del tiempo de inactividad y gestión de la producción en tiempo real. Una interfaz de pantalla táctil de fácil manejo permite al operario de línea un control de todo el proceso de envasado. Una conexión Ethernet enlaza con la base de datos y los programas de software del sistema SCADA y proporciona datos de diagnóstico, tendencias e información de gestión.
Principales Beneficios
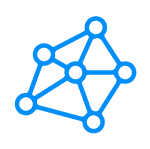
Más Flexibilidad
Adecuado para cualquier tipo de líquido. La misma Llenadora cubre una amplia gama de viscosidades y naturalezas de productos. Tiene capacidad para estar en contacto con productos peligrosos, corrosivos o inflamables (ATEX) para manejar líquidos que contienen alcohol, ácidos o bases. Desde bajos a altos niveles de pH.
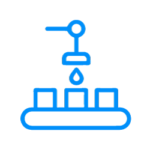
Mejor Estabilidad
La eficiencia en el llenado no se ve afectada por las ineficiencias en el diseño de la planta. El sistema controla la presión del producto en el interior de la Llenadora para garantizar el flujo óptimo a través de cada módulo de llenado.
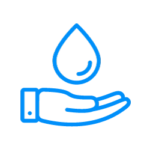
Precisión Mejorada
Control preciso de la dosificación en tiempo real. a dosis se mantiene constante desde la primera botella hasta la última del día, independientemente de las micro paradas de línea o cambios en la fórmula que afecten al líquido.
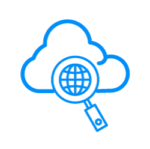
Gestión de la producción en tiempo real
Con el "seguimiento del tiempo de inactividad" y la gestión de la producción en tiempo real de Mengibar, el operador de la línea tiene control sobre todo el proceso de envasado. Las características incluyen el estado de la máquina, seguimiento del tiempo de inactividad con identificación de la causa raíz, monitoreo de calidad, alertas y notificaciones automatizadas, desempeño de OEE, análisis de tendencias significativo, consumo de energía individual, administración de seguridad, etc. Una conexión Ethernet enlaza con la base de datos y los programas de software del sistema SCADA y proporciona datos de diagnóstico, tendencias e información de gestión.
Principales características
- Fabricado para resistir: máxima durabilidad en entornos industriales.
- Precisión mejorada: Superando los estándares del mercado en precisión de llenado.
- Eficiencia del agua: Lavado avanzado con menor consumo de agua.
- Llenado versátil: De productos muy viscosos a muy fluidos.
- Diseño transparente: Racionalización del mantenimiento preventivo y las inspecciones visuales.
- Gama de alta velocidad: a partir de 100 botellas por minuto.
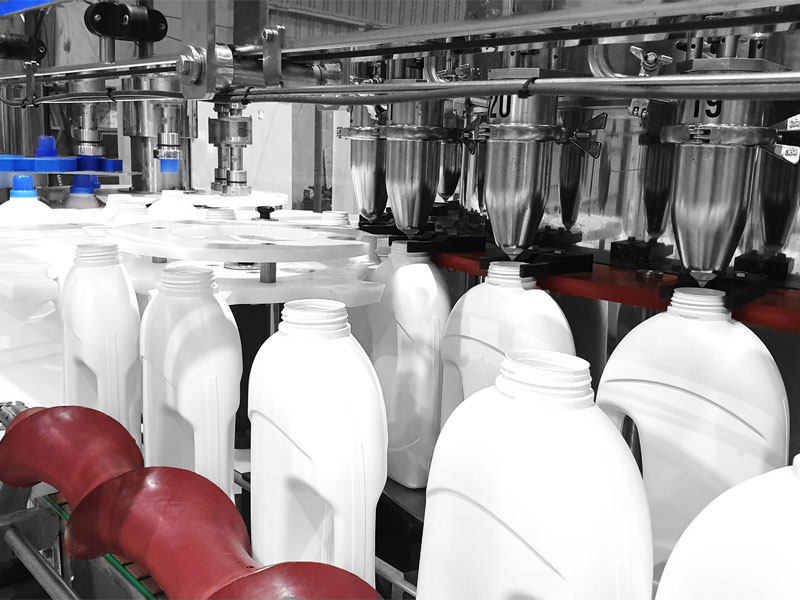
Fluidos
Espumantes
Viscosos
Corrosivos
Explosivos
Abrasivos
Mercados & Aplicaciones
Cuidado del Automóvil
Desinfectantes
Lavado de Ropa
Soluciones de maquinaria versátiles
Mengibar ofrece soluciones versátiles de maquinaria de llenado y tapado de líquidos diseñadas para manipular desde delicados productos de venta libre hasta materiales corrosivos. Nuestros equipos cuentan con una capacidad mejorada para contenedores de mayor tamaño, lo que garantiza una producción eficaz a cualquier escala.
Construcción para una resistencia superior a la corrosión
CORROSION-PROOF PERFORMANCE
Llenado de productos inflamables
EXPLOSION-PROOF
DESIGN
Ideal para líquidos sensibles en envases pequeños
OTC PRODUCT COMPATIBILITY
Llenado de botellas grandes